What is a Lost Time Injury (LTI)?
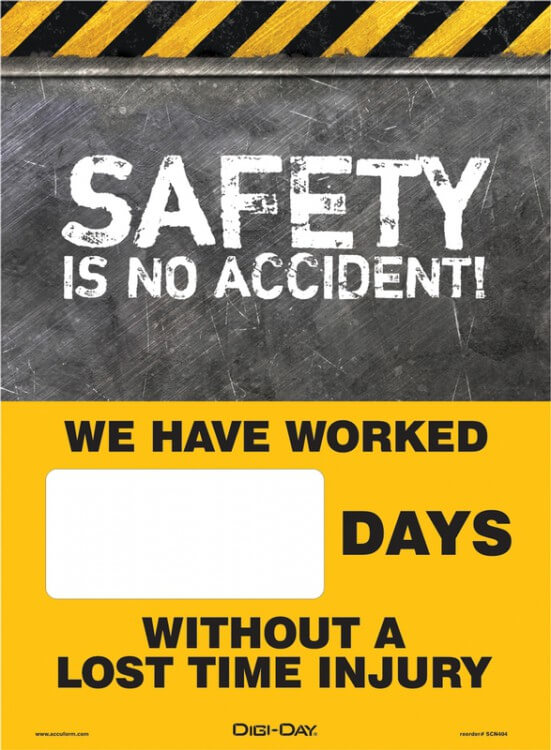
A Lost Time Injury (LTI) occurs when a staff member is hurt at work which causes them to be unable to complete their duties on the job for a minimum of one shift or workday. The LTI Frequency Rate (LTIFR) of a team is often used (rightly or wrongly) as the primary KPI or metric in measuring a company’s level of workplace safety.
‘Lost Time’ refers to the fact an incident or injury costs the organisation time and money directly and indirectly. Direct costs include the reduced productivity of the staff members effected as they put in leave claims, attend law suits and suffer from mental or physical injuries. Indirect costs can include machinery damaged from the incidents, worksite shutdown costs, government fine and reduced employee morale. Furthermore, if you have to replace workers, the ‘newbies’ are generally less productive as they try to gain experience.
Safe Work estimated work related injuries and illness cost the Australian economy $61.8 billion in 2013-14. Clearly, it is in the best interests of employees and employers alike to rally to reduce the LTI rate by focusing on safe work procedures every day.
What are common types of LTIs?
While there are hundreds of different types of lost time injuries that vary from industry to industry, the most common include:
- Back and neck strains/strains
- Lumbar disc displacements
- Ankle sprains
- Knee contusion
- Knee cartilage tears
How can I calculate my company’s LTIFR?
The universal measure of Lost Time Injury Frequency Rate is generally calculated by finding the number of lost time injuries per million hours worked over a certain period (often a financial year).
LTIFR = (Number of LTIs) / (Number of hours worked) x 1,000,000
Or, use the simple calculator below to discover your company’s LTIFR.
[calculoid id=56215]
5 ways to improve the LTIFR at your company
1. Don’t focus solely on LTI as a measure
Before you dive too deeply into strategies to improve your LTIFR, there is a disclaimer you should consider.
It is common that a health and safety professional emphasizes that you shouldn’t be too preoccupied with outcome-based performance, as this can actually increase the hazards workers face on the job. People may be driven to falsely report on the LTIFR by not reporting incidents or over reporting the number of hours worked.
LTIFR is a lagging indicator of safety, which means it measure past performance. Thus, it doesn’t give your company any indication of actions to take in the future to improve the safety of your workplace. You should report on a variety of metrics and measures, some leading indicators such as the percentage of employees that have completed WHS training, and some lagging such as LTI, so you can get a clear picture of the safety of the environment you staff work in now and in the future.
2. Get in professional help and training
While it may initially seem like a large investment, getting in a WHS consultant is one of the more effective ways to develop and plan and strategy to reduce your Lost Time Injury rate. They will take an ‘outsider’s’ audit on the safety and ergonomics of your workplace which is generally more unbiased and scrutinizing than one from an employee who works in the business every day. Auditing should be at least an annual exercise.
Ensuring your employees are sufficiently trained and educated about injury prevention and safety. You may need to schedule regular mandatory educational sessions to keep you team up to speed with developments in the environment and to keep safety at ‘front of mind’ in view of developing a ‘safety culture’ within your team. Any employee using machinery should be educated and screened about the procedures they are required to complete. Something as simple as group warm ups before a shift can help reduce the LTIFR at your company.
3. Ensure your team has compliant and suitable PPE
While it may be tempting for your company to minimise costs when it comes to PPE procurement, purchasing quality equipment that will keep your staff as safe as possible. Purchasing compliant and suitable PPE may cost more, but the reduction it can bring in lost time injuries will mean the return on investment is well worth it. Partner with a PPE provider that has a thorough understanding of the requirements and regulations around your industry.
4. Ensure you aren’t understaffed
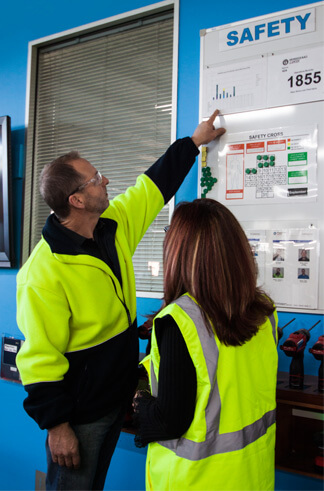
While this may seem obvious, overtime hours because of understaffed teams increase the stress on staff. Tired employees are more likely to cut corners and work ‘sloppily’, thus increasing their chance of getting injured on the job. Effectively managing the staffing schedule and putting on casuals or part timers can help reduce workload and reduce your LTIFR.
5. Have a LTIFR scoreboard
A scoreboard displaying you current LTIFR rate is a very visual method to drive the importance of this number amongst your team. As we discussed in point number 1, however, don’t only push this metric. Your scoreboard could include a range of other measures that will help you drive your safety culture and reduce lost time injuries at your workplace.